Understanding Pipe wall thickness charts and formula for calculating pipe thickness
The determination of a pipe’s wall thickness is of fundamental importance in pipe engineering especially in the area of piping systems that are to be exposed to certain internal pressures and external loads. This guide details the methods of thickness calculation of pipes with an emphasis on the principles outlined in the ASME B31.3 code.
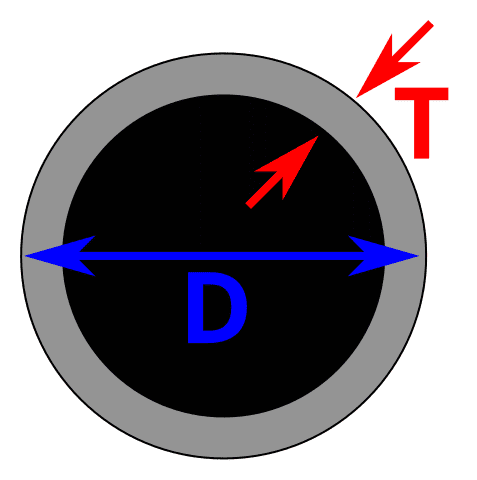
How to calculate thickness of pipe | How to calculate pipe wall thickness ?
The wall thickness of a pipe is of utmost importance in maintaining the stability and safety of piping systems. Since pipes carry fluids, they have internal pressure and when the wall thickness is not enough, failures such as leaks and burst may occur. The most common equation applied for determining the minimum allowable thickness is based on Barlow’s formula, which is,
Pipe thickness formula | Formula for calculating pipe thickness
t = PD / 2(S+PY)
Where:
- t = required wall thickness
- P = internal pressure (psi)
- D = outside diameter of the pipe (inches)
- S = allowable stress value for the material (psi)
- E = longitudinal weld joint quality factor
- Y = coefficient based on temperature and material properties
Key Parameters Affecting Pipe Thickness
Several factors influence the required thickness of a pipe:
- Design Pressure: Higher internal pressures necessitate thicker walls to withstand the stress.
- Design Temperature: Certain materials lose strength as temperature rises and hence require increased thickness.
- Pipe Material: The stress requirements vary from one material to the other; thus under similar conditions, a range of pipe configurations for carbon steel and stainless steels would be different.
- Corrosion Allowance: Over time, some pipes will be caked with corrosion which may necessitate additional pipe thickness.
- Manufacturing Tolerance: To accommodate the specified safety requirements usually it is a small percentage of thickness.
Pipe thickness calculation | Pipe wall thickness calculation
Steps for calculating pipe thickness | Step-by-Step Calculation
To illustrate the calculation process, consider a seamless carbon steel pipe with specific parameters:
- Material: ASTM A106 Gr. B
- Nominal Pipe Size (NPS): 4 inches
- Design Pressure: 1200 psig
- Design Temperature: 500°F
- Corrosion Allowance: 3 mm
- Mill Tolerance: 12.5%
1. Calculate Pipe Thickness using Barlow’s formula:
- Convert units if necessary (1 inch = 25.4 mm).
- Substitute values into the formula. For example:
t = (1200×114.3) / 2(19000+1200×0.4) = 3.52 mm
2. Add Corrosion Allowance:
- Total thickness after adding corrosion:
tc = t+c = 3.52+3 = 6.52 mm
3. Add Manufacturing Tolerance:
- Calculate required thickness considering manufacturing tolerance:
tm = tc / 0.875 = 6.52 / 0.875 = 7.45 mm
4. Select Standard Pipe Thickness:
- From ASME B36.10M, choose the next available standard thickness that meets or exceeds this calculated value, which would be approximately 8.56 mm or Schedule 80.
Pipe thickness chart | Pipe schedule and thickness chart | Pipe wall thickness chart
This is a complete thickness table for pipes in accordance with the standards of ASME B36.10M and B36.19 which provides dimensional, wall thickness, and weight information for all range of pipe sizes. This chart includes common schedules and their corresponding specifications.
Pipe Thickness and Schedule Chart
NPS (inches) | Outside Diameter (OD) (inches) | Wall Thickness (inches) | Schedule 5 | Schedule 10 | Schedule 20 | Schedule 30 | Schedule 40 | Schedule 80 |
---|---|---|---|---|---|---|---|---|
1/8 | 0.405 | 0.049 | 0.065 | 0.109 | 0.147 | 0.188 | 0.237 | 0.337 |
1/4 | 0.540 | 0.065 | 0.088 | 0.119 | 0.154 | 0.203 | 0.254 | 0.370 |
1/2 | 0.840 | 0.109 | 0.120 | 0.147 | 0.203 | 0.254 | 0.300 | 0.430 |
3/4 | 1.050 | 0.113 | 0.120 | 0.154 | 0.218 | 0.276 | 0.300 | 0.480 |
1 | 1.315 | 0.133 | 0.140 | 0.179 | 0.237 | 0.300 | 0.364 | 0.506 |
1-1/4 | 1.660 | 0.140 | – | – | – | – | – | – |
1-1/2 | 1.900 | 0.145 | – | – | – | – | – | – |
2 | 2.375 | 0.154 | – | – | – | – | – | – |
2-1/2 | 2.875 | 0.203 | – | – | – | – | – | |
3 | 3.500 | 0.216 | – | |||||
3-1/2 | ||||||||
4 |
Additional Information
- With each increasing schedule number, the wall thickness tends to increase; thus, decreasing the internal diameter due to the thicker walls.
- Wall thickness values are essential in exercises related to rating the pressure and strength of pipes in different utilizations.
- This chart is mainly concerned with the standard specifications for pipes made of carbon steel regardless of other materials having other specifications.
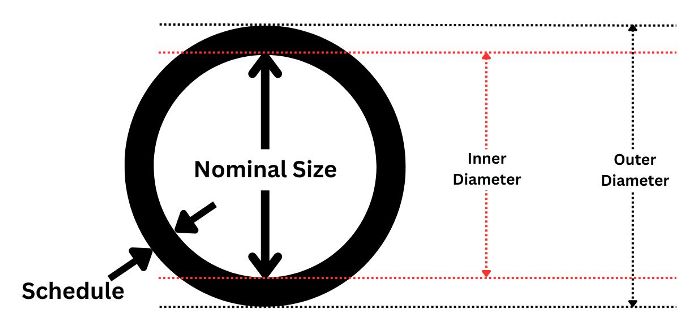
Reference Standards
The data provided in this chart is based on the following standards:
- ASME B36.10M: Welded and Seamless Wrought Steel Pipe
- ASME B36.19: Stainless Steel Pipe
For detailed specifications and additional sizes, it is best that official documents or engineering libraries be consulted as they provide extensive tables for the many dimensions and weights of pipes.
This chart is a simple tool for designers, constructors and maintenance engineers that assists in the piping systems layouts, installation and assuring
Pipe Thickness Chart PDF Download
(Credit: Octal Steel)
Conclusion
The most important aim in engineering practice that needs to be addressed is that of determining the thickness which guarantees the safety and reliability of the piping systems. Assembling a set of appropriate formulae systems which have some parameters, it is possible to compute relevant wall thicknesses meant for fulfilling the service requirements of the piping, and comply for instance with ASME B31.3.
This both lessens and even eliminates the threat of failures and also enables better materials use and thus improves the economic design solutions in the varied industrial applications.